A green device for a green world
Students design and build a device to collect solar, wind and hydroelectric power
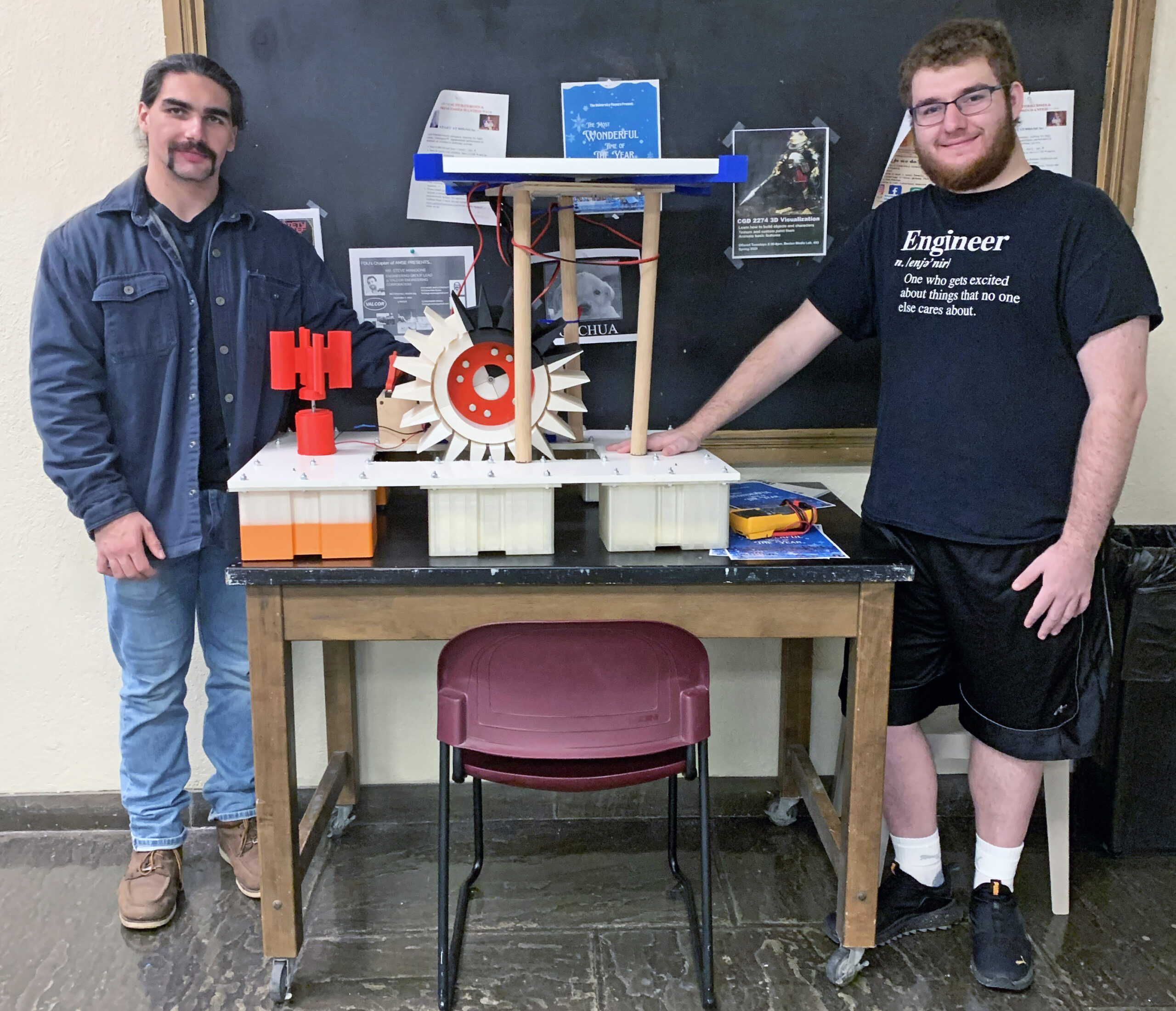
Steven Pini-Duin, left, and Sam Shipley, right, flank their green energy device. The red turbine collects wind energy, the red and white water wheel collects hydro energy, and the top panel collects solar energy.
By Kenna Caprio
Back in the fall, Steven Pini-Duin, a senior mechanical engineering technology major, and Samuel Shipley, a junior mechanical engineering major, dropped their green energy device into the Hackensack River behind Becton Hall and waited to see if their second prototype would work.
It did.
“The device floated, collected solar energy and the water wheel spun. The wind turbine didn’t spin because the air was still as can be that day. We were able to charge up the battery and store energy,” says Pini-Duin.
The device — meant to be fixed, floating in one spot, but active from all directions — features a solar panel, a wind turbine and a hydro-electric component.
“That first day the device collected over 340 watts of energy, which is equivalent to running a 10-watt lightbulb for 34 hours straight,” adds Shipley.
Before embarking on this project together, a class assignment of sorts, the two students were acquaintances. Pini-Duin opted to submit a research proposal for a student grant through FDU rather than write a 20-page paper for one of his classes. “I wanted to do something that I could add to my résumé,” says Pini-Duin. “The world we live in is turning green.” He brought Shipley on board the project, praising his computer-aided drafting (CAD) skills. The two received a grant under FDU’s Undergraduate Mentored Projects: Informing Decisions and Actions on Climate Change.
“We knew we wanted to manufacture a pretty ambitious device. I did the practical administration side and dealt with the feasibility of the device and Sam did the design and manufacturing side,” says Pini-Duin. Shipley, the head student engineer at Becton Hall, manages the 3D printing lab. Eighty percent of their device is 3D printed. It also uses bidirectional electric motors.
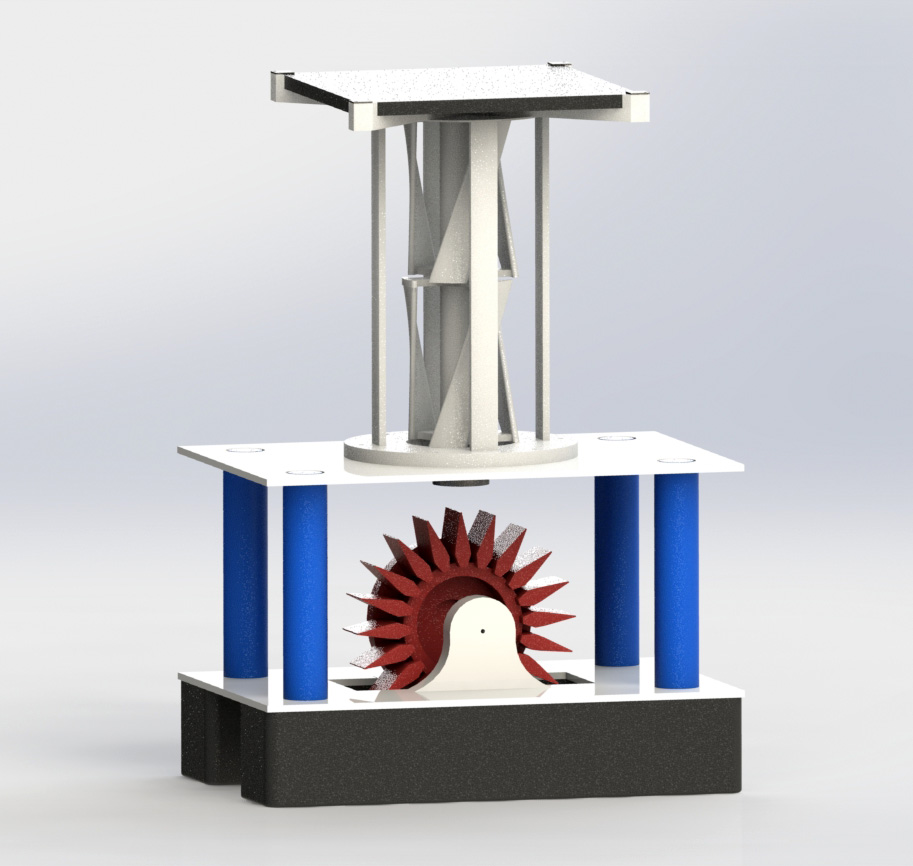
The initial project design.
“It’s a three-stage multi-energy collection device that is a modular system, so it can be paired with more devices, to increase energy collection,” says Shipley. “All of it was designed from the perspective of collecting as much energy from the Earth possible.”
Any questions they had, they went to Christopher Stubbs, assistant professor of mechanical engineering and mechanical engineering technology, and their mentor. “Professor Stubbs is very involved with upperclassmen studying mechanical engineering,” Pini-Duin says. “He just kind of turned into our adviser!”
For inspiration, Pini-Duin and Shipley looked around the world at green energy collection.
“For example, there are roadways in China where cars create a cross breeze between the highways. There are fans set up to collect that energy as the cars pass by,” Shipley says.
“The rotational energy that’s created charges the streetlights which are used at night,” adds Pini-Duin.
With that in mind, they contacted the NJ Meadowlands Commission, and went to River Barge Park and Marina in Carlstadt, N.J., to gather more information.
“The goal could be for these devices to power beacon lights at a marina or sconces on the marina footpath. Or it could even be to power a power washer or to plug your phone into. We want it to do multiple things at once,” says Pini-Duin.
And they want people to be able to make these devices on their own and easily. “All the plans and 3D-printed models are free to the public, and the assembly uses tools that most people already have. This is a device that anyone with a 3D printer and some simple tools can build at home very inexpensively,” adds Stubbs. “Such a grassroots approach to renewable energy is novel and really promising.”
The entire process, from initial funding to prototype testing, took them two-and-a-half semesters.
“We’re going to continue to research and develop the device. As we learn more, the device will improve,” says Pini-Duin. “For now, we’re focused on our senior projects.”
As outgoing president of FDU’s chapter of the American Society of Mechanical Engineers (ASME), Pini-Duin wanted to leave a legacy as part of his capstone project.
“We spent the last year designing and manufacturing catapults. Our competition in April had a huge turnout. My capstone is the life cycle of a project from the project manager’s perspective — from inception to closure. It starts with the competition idea and proposal and then follows the process from receiving funding, to administration, to design, to manufacturing and to competition,” says Pini-Duin. “My goal was to leave a big mark on the school and put the ASME professional organization on the map.”
He’s already accepted a job after graduation as a project engineer for Kiewit, working with infrastructure.
Meanwhile, Shipley, though a junior, has already been at work on his senior project for two years.
“It’s a drone that will travel through interstellar space and send back samples and deposits of either moons or things with atmosphere. I’m most interested in heat gradients and thermoelectricity. Everything I’ve been doing is all green. There’s no fuel in it. It’s all electric.”
Both plan to focus broadly on green energy in their careers and want to develop more efficient and optimized alternative energy options.
“Research allows for student-guided learning, which helps students feel in control of their development, in turn teaching them valuable skills such as independence, confidence and responsibility,” says Stubbs. “My favorite part of working with them was seeing how they learned from each other’s individual expertise. Steve is excellent at managing a project, and great in the machine shop using traditional manufacturing methods like the lathe, mill and band saw. Sam, on the other hand, is an expert at 3D-modeling and design, as well as advanced manufacturing methods like the 3D printer, CNC machines, and laser cutters. Getting to see them teach each other and become more well-rounded engineers was great to witness.”